
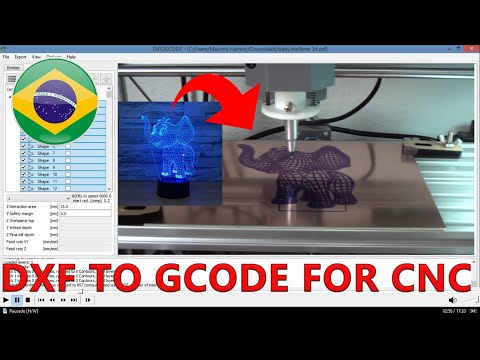
All of a sudden when I reloaded a program I successfully used before it does this. This has never happened to me before when running the same programs with the same setups and motor speeds. Then after another 15 minutes or so, all the motors stop again. I stop the program and after a couple of minutes when I try to restart the program all the motors start working again. About 15 minutes into the milling process all the motors (2-X axis, Y axis and Z axis)stop but the program continues to run. Additional Information: I need to clarify my situation a little better after going to my shop and trying to run another program on Mach 3. Sometimes Mach3 will show a status when something goes wrong, but in cases where the motor is stopping due to its torque limit, then that would not be shown in the status. It's probably not the limit switches since that would cause a stop to the entire motion of the cnc router or laser machine. Recommended action would be to thoroughly inspect the wiring. It can also be a loose digital wire from the controller board to the driver. This could be a loose wire, or a chafed wire (or two shorting together). There is a wiring issue with the wiring from the driver to the motor. Recommended action is to lower the velocity and/or acceleration, and/or lower the feedrate when cutting.

This is where the control software is trying to move the stepper motor too fast (velocity, or too fast too quickly, acceleration) and the load against the stepper motor (inertia of the machine, or the material against the end mill while milling). The motor found its limiting torque (usually comes with a not-so-pleasant sound). If one of your stepper motors decides to stop moving and the others are moving during a CNC milling or laser cutting job, then there could be two things that could be causing this.
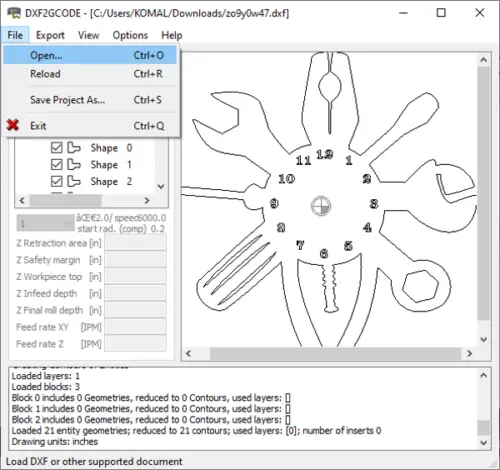
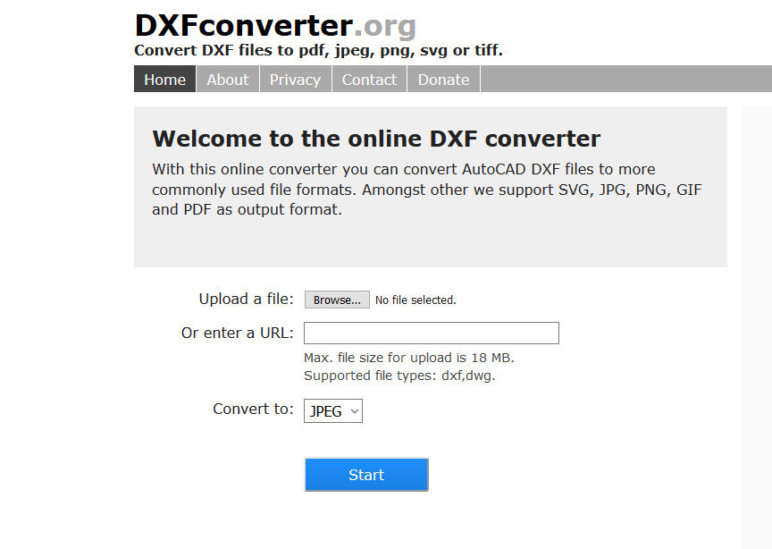
Other Possible Solutions to this Question These machining operations are what is converted into Gcode. A CAM program, like CAMBAM, Cut2D or other Vectric software, MechCAM, etc that allows you to apply machining operation to the dxf geometry. This information does not exist in the dxf file. There is also the speed to cut the geometry, how deep to cut the geometry, etc. The cutting would need to be half the diameter of the end mill from the geometry so the edge of the end mill cuts along the line. You may want to cut on the inside of the circle, or the outside of the circle. For instance, take a circle that may be in the dxf. A dxf file is simple geometry and does not contain enough information to properly control a machine. Gcode is a set of instruction on how to cut geometric features which has numerous parameters for control. There really isn't a program to directly convert a dxf (drawing exchange) file to gcode instructions. DXF file to a G-Code file to use with Mach4. What is the best program to use for converting a.
